BIOVECTRA combines 50+ years of premier CDMO experience with the latest fill/finish technology and facilities. The result: quality products, time and time again, across a range of different modalities.
The sterile fill/finish process is the final critical step for many small molecule and biologic drugs. It occurs at a high-stakes stage of manufacturing after significant time and resources have been invested in a given batch, leaving little room for error.
To ensure each drug is reliably filled––contamination-free––manufacturers require a dedicated facility and staff who understand the need for rigorous processes and quality control.
With our new sterile fill/finish facility, BIOVECTRA can help overcome challenges associated with a range of sterile fill/finish vials, offering a flexible approach and fast turnaround times. Explore our capabilities below and then contact our experts for further details.

Catering to Small-to-Mid-Sized Manufacturers
Our facilities best suit clients with high-value products seeking to fill 20,000 vials or less per batch. Drug types processed include recombinant and synthetic proteins, peptides, nucleotides modalities–including mRNA, oligonucleotides, siRNA, pDNA–gene therapies, and vaccines.
Aseptic fill/finish of biologic drugs comes with unique considerations to address the fragility of these compounds. We’re equipped to serve a range of newer modalities, including gene therapies, mRNAs, and plasmids. Our industry-standard instrumentation gently processes products at room temperature; however, for more sensitive products, we can provide temperature control of the bulk product and shortened fill times to maintain the product at cooler temperatures when necessary.
State-of-the-Art Biomanufacturing Center
- 36,000 square feet of new, state-of-the-art manufacturing space
- cGMP, ICH Q7 and Q10, and Annex 1-compliant facilities
- Two fully automated Cytiva/VanRx (SA-25) aseptic fill/finish suites
- Up to 40,000 filled vials per day
- Semi-automated inspection process
- Press fit closure system
- Fill systems are entirely single-use
- Qualified fills for 10R and 2R fill sizes
- Automated equipment can be adapted for pre-filled syringes
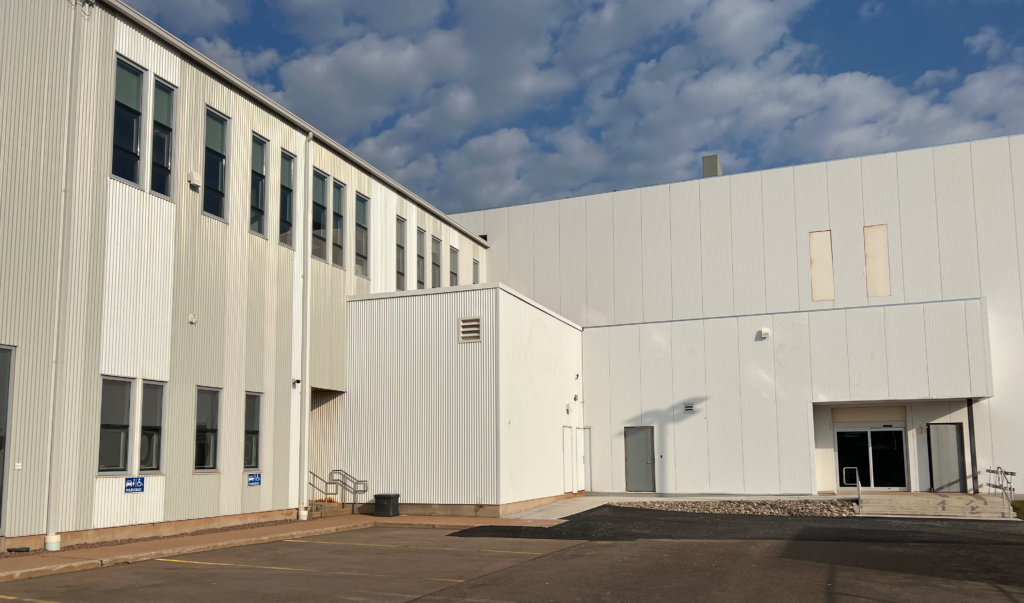
Fill/Finish at Any Stage of Development
Customer-Centric Approach
No need to source multiple vendors at different stages of your clinical trial. BIOVECTRA offers manufacturing and aseptic fill/finish at all stages of the clinical development process. Our extensive expertise in providing CDMO services gives us the know-how to be as flexible as you need us to be while offering fast turnaround times.
One-Stop Manufacturing
Your product is unique, but your aseptic filling needs are not. At BIOVECTRA we know how to leverage this to conduct fill/finish projects with ease. We have the staff, facilities, and technology necessary to offer full-service capabilities, meaning that all analytical testing, quality assurance release, regulatory support, project management support, and more are delivered in-house.

Accelerate Your Path Towards Clinical Readiness
Reliable Fill/Finish Capabilities
Our systems are fast and flexible. Using automation and single-use closures and containers, we expedite project timelines while nearly eliminating the risk of particulate failures and the introduction of microbials. Regulatory excellence is our highest priority: we have a strong record of successful inspections by Health Canada, the U.S. FDA, and the Japanese PMDA.
Commitment to Service
We always strive to exceed expectations. We care about our customers’ products and their patients. We build deeper partnerships thanks to robust communication and a high level of touch throughout the manufacturing process.
Industry-Leading Instrumentation
Our facility houses two VanRx instruments that can be run in parallel for faster turnaround times. Benefits of these instruments include:
- Gloveless isolator technology that eliminates the need for manual intervention
- Single-use technology for all product contact parts to reduce the risk of contamination
- Method-based recipe programming of internal robotic controls that ensures reproducibility and consistent vial dosing across the batch
- Separate material transfer isolator and filling isolator that allows for seamless batch production (up to 20,000 vials/day per filler)
- Statistical weight check with 100% verification of filled vials at run end to ensure reproducibility and minimal product line loss
- Environmental monitoring compliant with Annex 1 that uses volumetric air sampling, avoiding challenges associated with settle plates
- Accurate fill process: from 0.2 –2 mLs instrument has 1.5% accuracy; above 2 mLs it has 0.5% accuracy
- Inert gas overlay capabilities
- Light-sensitive fills are available. Please inquire if you have a light-sensitive product.
- Prefilled syringe manufacturing capabilities that use press-fit closures to control bubble size
Partner with Us for Your Next Fill/Finish Project
With our state-of-the-art facility, we’re ready and able to cater to your fill/finish needs with the flexibility, speed, and quality you expect from a top-tier CDMO. If you’ve developed your own nucleic acid or large or small molecule drug that requires aseptic fill/finish manufacturing, we’re the experts you can call and trust. We can accept technology transfers and/or have platform processes available.

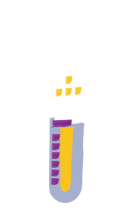
Process Development
Demonstrated experience in process development and characterization, offering phase appropriate solutions and rapid optimization.
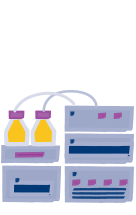
Analytical Development
Targeted analytical support from early development to validation of commercial processes and continuous process verification, all along the life cycle of your program.
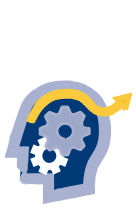
Tech Transfer
Dedicated tech transfer teams ensuring a seamless transition from development to manufacturing - collaborating with our clients with a problem-solving mindset.
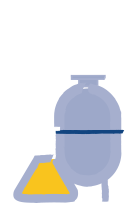
Clinical Development
Supplying our clients with pre-clinical and clinical material to enabling them to move quickly and cost-efficiently through the clinical phases.
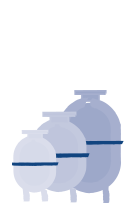
Scale-Up
De-risking our client’s programs by effectively managing the transition from lab to pilot to manufacturing scale.
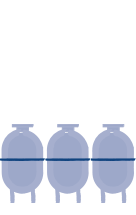
Commercial Scale
A proven history of commercial manufacturing partnerships growing alongside our clients. Effective collaboration increasing speed-to-market.